Pelleting
The raw material must reach a few factors before it is possible to make pellets. The raw material skuld have a dry content of 85% and size of less than < 3mm.
From raw material to Pellets in the facilities different parts
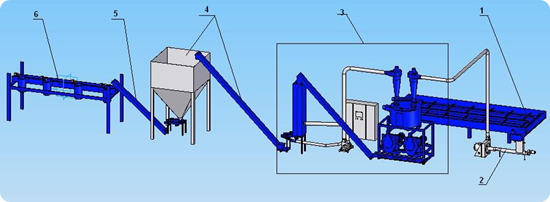
1. Saw cut dust storage with feeding
Automatic feeding for saw dust
2. Hammer mill with a fan
Material larger than 3 mm should be ground down in the hammer mill.
A hammer mill which grinds cutter chips down to the size of sawdust. The container and feeder are located below the grinder. They collect and store the ground material. Sensors detect the level in the container so that the flow of material can be automatically controlled via PLC. Frequency control and sensors control the level and flow of material in the container.
3. Pelleting
A high pressure is needed to force the material through the die. If the material is too damp, the water starts to evaporate and the feeder rolls slip, causing high friction between the die and the rollers. This in turn generates heat which, if excessive, may cause fire.
The pellet press consists of a die and two feeder wheels. The wheels are mounted on a driving fork. The pellet
press is automatically fed. This means that the flow of material is controlled by frequency control of the feeder
screw in the feeder.
After the press, the hot pellets drop into the elevator.
The elevator buckets raise the pellets to the cooling tower.
In the cooling tower, a fan cools the pellets to a suitable temperature for storage. A sensor control the level in the
cooling tower and the discharge of cooled pellets.
4. Silo and Sieve
Separation of saw dust from pellets. It sifts out any small pieces that accompany the finished pellets.
5. Transportband
Transportation of the pellets to the filling station
6. Filling Station
SPC offers small sack filler or large sack filler as spare parts. The pellets are automaticly filled in sacks, ready for sale.